Coolington Barn
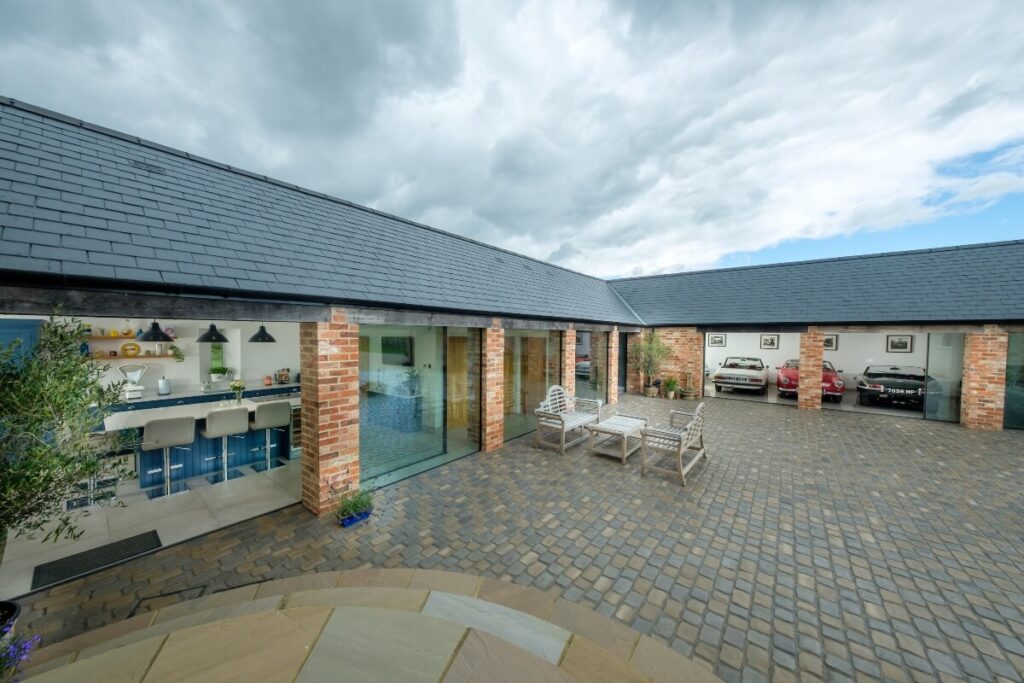
Barn Conversion and Re-build of ‘hovels’ (open sided small barns) around the yard were granted permission. The hovels created space for more bedrooms and garaging/workshop.
Can I extend a barn conversion?
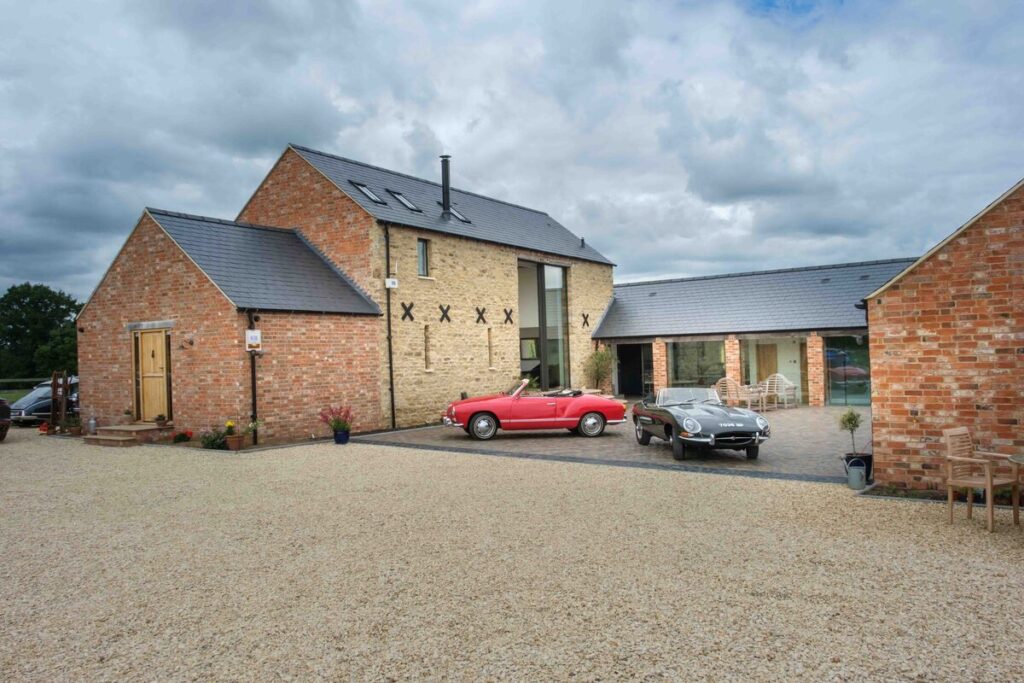
Can I extend a barn conversion? In general planners have a dislike for barn conversion extensions. Most councils have policies that effectively exclude them. But there are some exceptions. Generally, as barns are in open-countryside, new-build is not an option. However, re-building former barns can sometimes be granted with significant justification to the planning authority. […]
6 Self-Build Plots
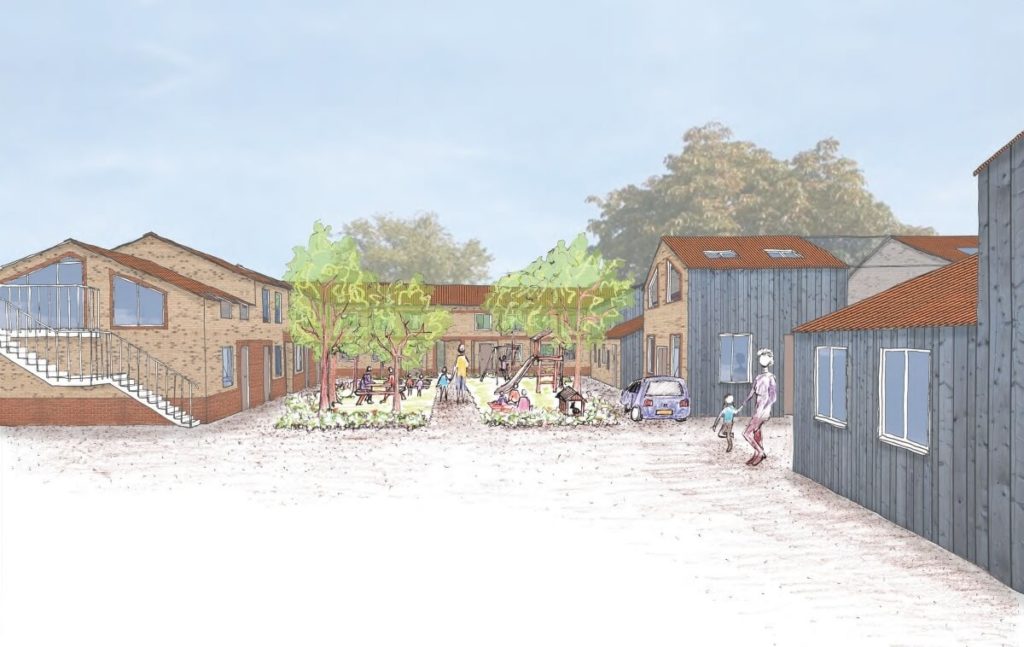
We have been working on creating self-build plots for family members of a landowner and for market sale.
Replacement Farmyard Housing Project

We were approached by a developer looking to build eight houses on the site of an old farmyard in Cambridgeshire. The intention was that young families looking to move out of the city could settle down here.
Small Extension to Maximise Space and Light
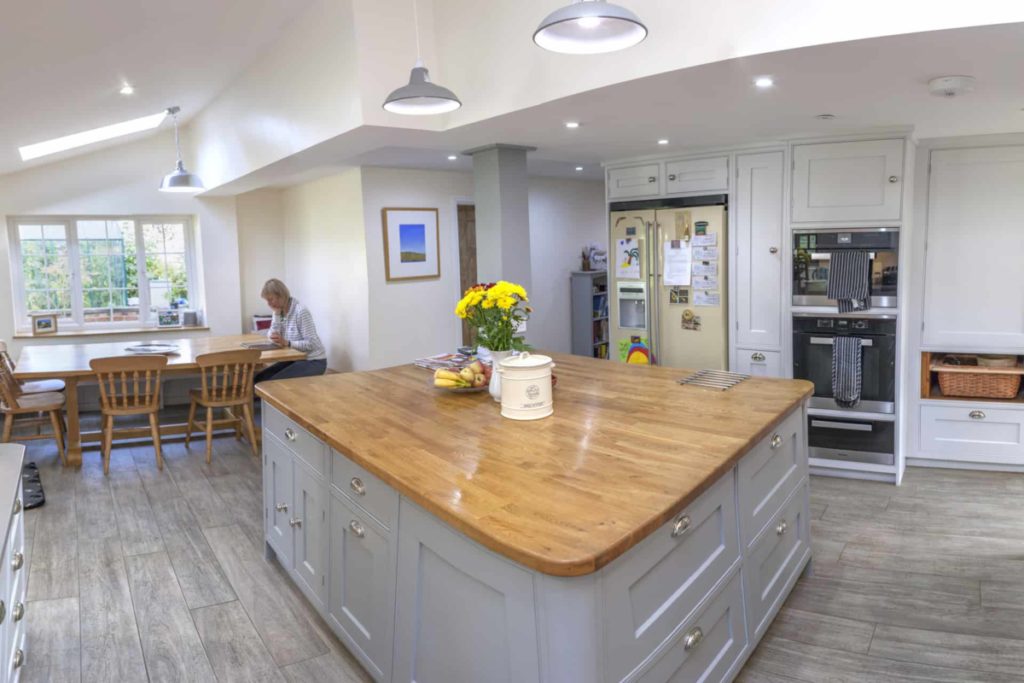
This small extension had the sole but vital purpose of maximising space and light. The existing house was dark. Particularly the kitchen, which was small and difficult to access from the rest of the house. Additionally disabled access and a wet room were needed.
Cottage Remodel
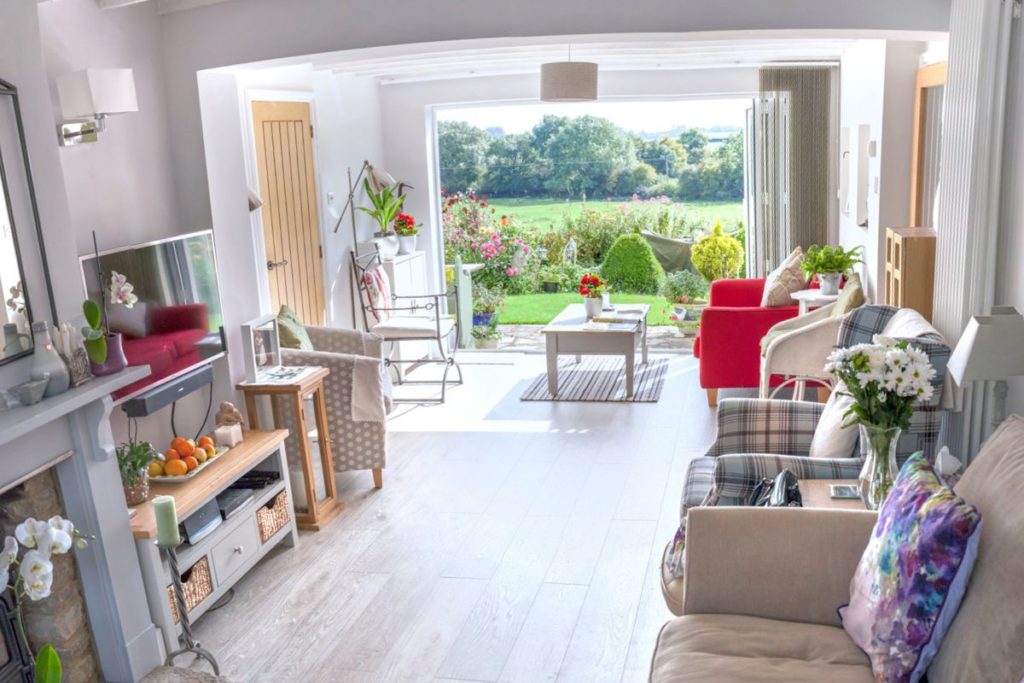
This project was about increasing light to an existing rear extension and the rooms within, as well as maximising access to the beautiful garden and view beyond.
Modern Extension and Disabled Access
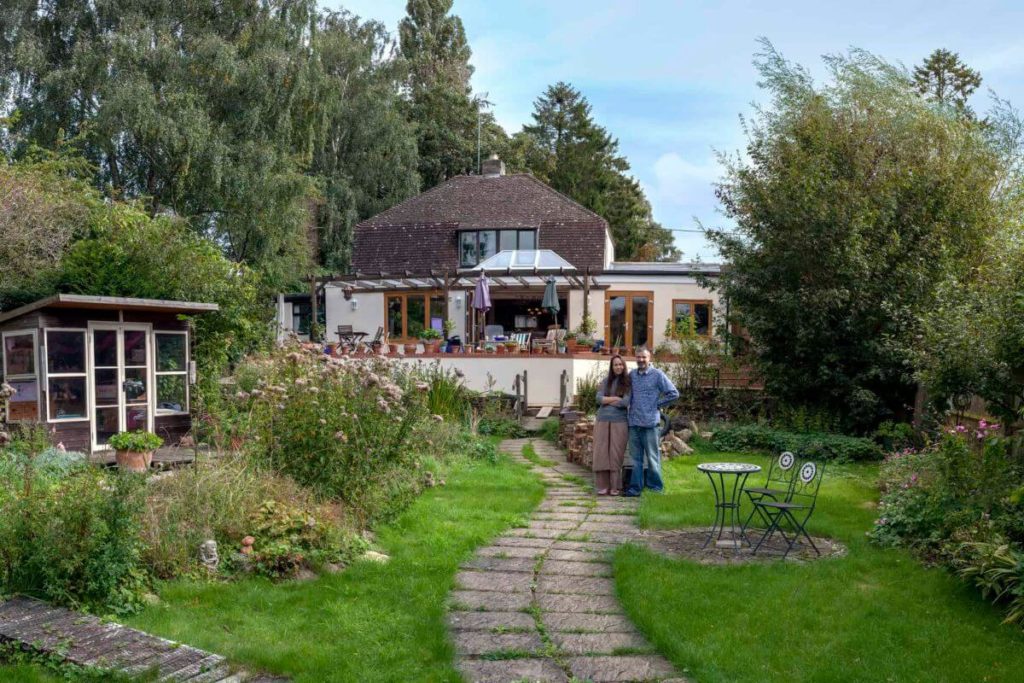
This modern extension required disabled access, due to illness and the necessity to potentially accommodate a wheelchair in the future. The garden was steeply sloping so we carefully designed a ramp to make access beautiful and practical (with raised herb beds) rather than clinical.
Bungalow Remodel
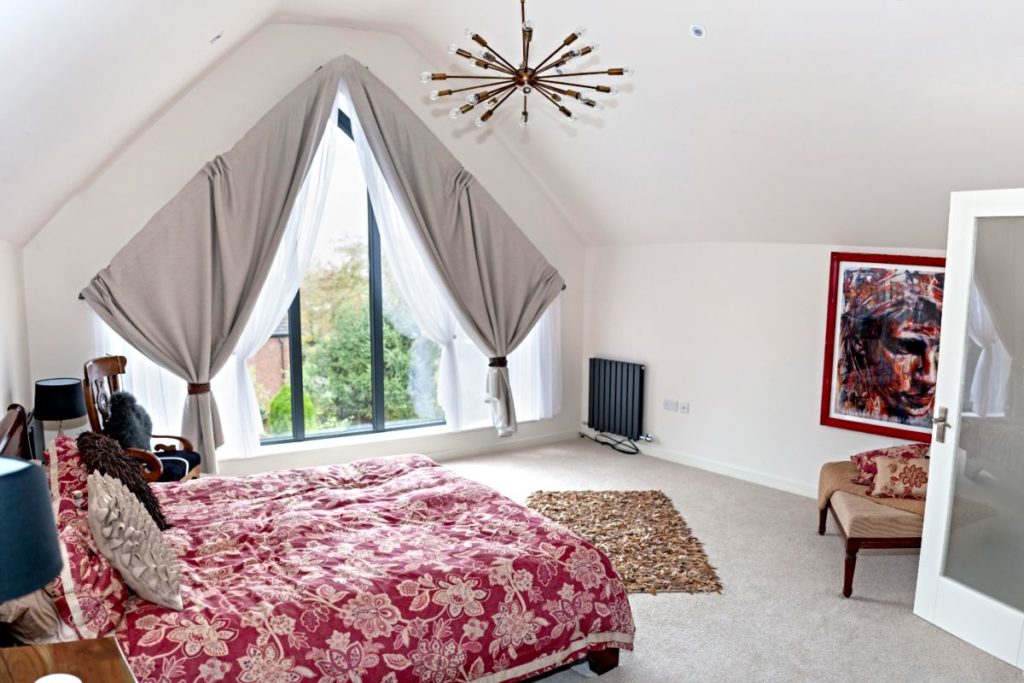
This bungalow remodel almost doubled the value of the clients home and a great reminder that you don’t have to build a new house to achieve your dream home. It is possible to create the same feeling with a remodel.
Kitchen and Vaulted Garden Room
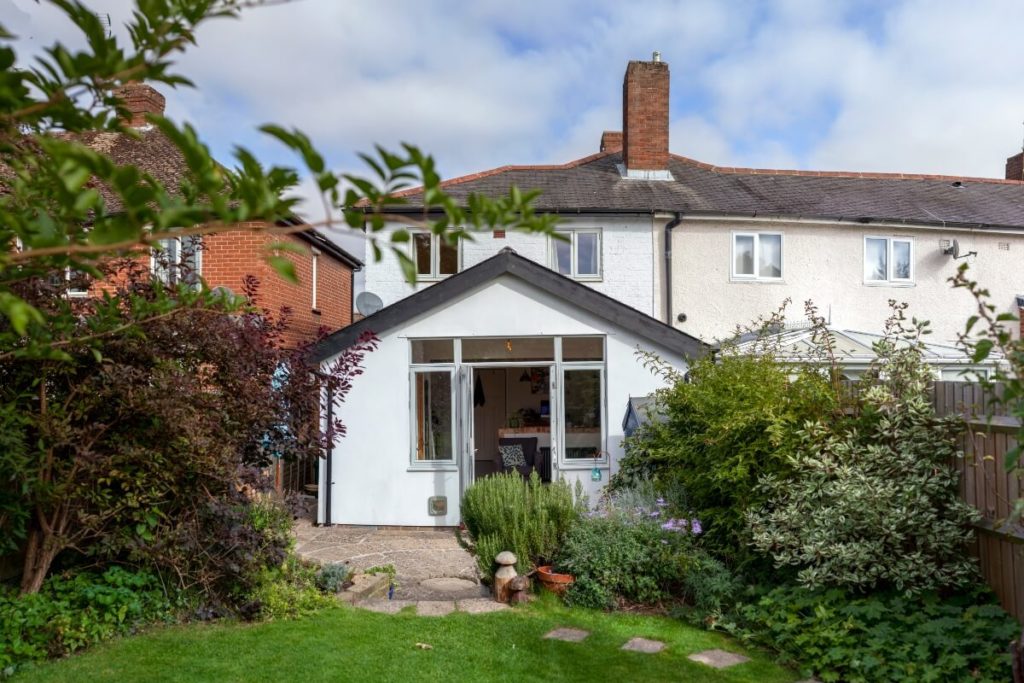
This transformation of a chilly conservatory and dark kitchen into a lovely, light, warm, vaulted garden room and kitchen also saw a complete redesign of the garden. The main aims being to increase the feeling of space and light, maximise views to the garden and make it warm in winter.
MODERN BARN CONVERSION AND RE-BUILD IN OXFORDSHIRE
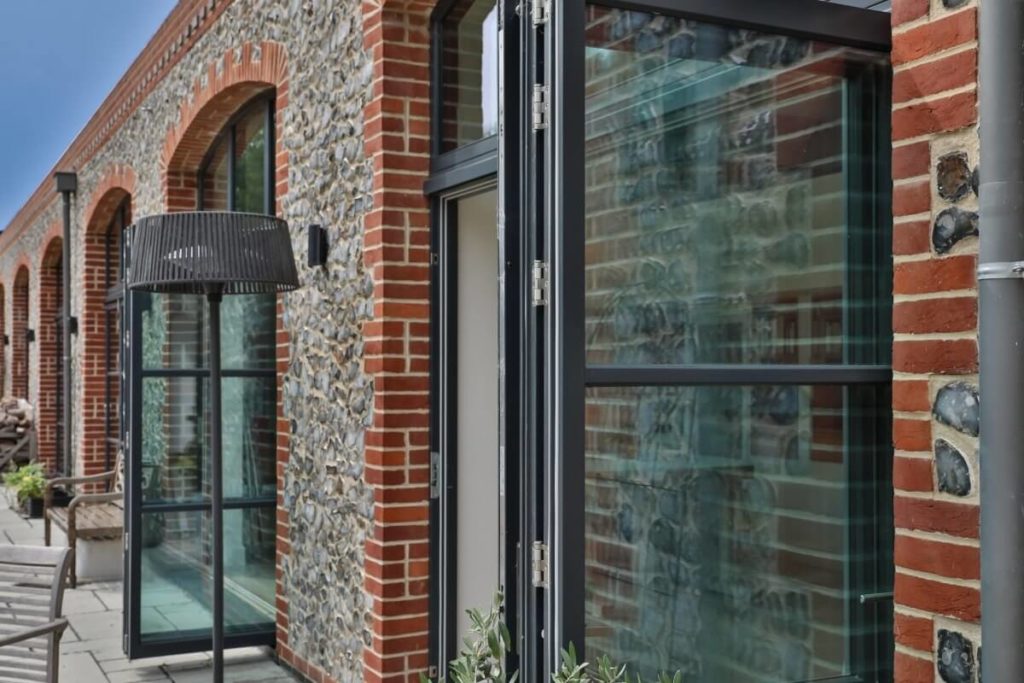
Converting these stunning barns were almost entirely a rebuild – a big project but well worth the effort!